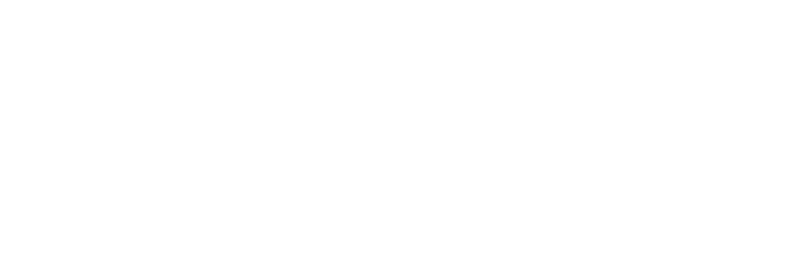
Call: 01234 765308
install and maintenance.
CECIL AND LARTER CASE STUDY
from Premier Garage Equipment
Images show reparing the floor for the inground scissor lifts
About our client
Project brief
The project brief was to design and install new specialist Volvo VRE garage workshop equipment including three inground short scissor lifts in the VRE bays and two 2-post lifts in the Andon bay.
VRE stands for Volvo Retail Experience – a highly refined workshop system and process which is unique to Volvo. This means when a customer books their vehicle into a workshop that has been fitted with a VRE bay it enables up to two technicians to work on the vehicle at any one time to speed up waiting times and ensure the ultimate customer experience from beginning to end. The VRE equipment is supplied directly by Volvo via a sophisticated parts system and includes all walling, cabinetry and tooling finished in corporate branded colours.
The workshop space already existed and was cleared to make way for the build. We split the six-week project into two stages; the first to include all enabling works and the second for the fitting out of all new equipment. We were on site at intervals throughout the six-week installation period working closely alongside the builders to ensure that everything ran smoothly.
Image shows installation of 2 post lifts in the Andon Bay
Was this project challenging?
The short timescale of just six weeks meant less downtime for the workshop so that it could get back up and running to full commercial capacity as soon as possible. This meant we had to schedule everything carefully and ensure that all equipment and people were on site when they were needed.
We were also faced with groundwork complications at the outset of the project caused by underground cables in the building, installed by a previous occupant. This meant that what should have been a textbook installation required serious modification. We had to excavate the cabling and associated steelwork before we could make the ground ready for installation. This was unexpected and given the short timeframe, could have thrown the project off course. However, to overcome delays we ensured all the products, materials and resources were in place before commencing the project. We also worked very closely with the other trades teams involved. This was achieved by having a project manager on site who co-ordinated the electricians, flooring contractors, groundworkers and construction workers through to completion.
The final complication was the limited width of the workshop from left to right. Therefore, to ensure our design would function correctly when installed, with technicians working in the space day-to-day, and would comply with health and safety standards, we mocked up our design in real-life before we were satisfied that the installation could proceed. We placed tape on ground to mark out the bays and used actual vehicles to move in and out of the space. The mock up enabled us to see how we could reduce the width of the VRE walling to maximise the workshop space. In saving 100m per side on the walling design and construction it enabled the gangway accessing the lifts to be increased by 200mm. Although this is only a small measurement is actually made a huge difference to what was already a tight turning circle with the intrusions of structural columns.
What next?
Following a few issues with sectional overhead doors failing to operate correctly during the project, which we repaired and serviced, we now also expect Cecil and Larter to sign up to a door servicing contract to ensure this equipment doesn’t fail again in the future.
Image shows electric vehicle bay
“This was a tricky project with various complications and short timescales which was handled brilliantly by PGE. They are never deterred or phased by a challenge and they approach every job with a highly professional attitude and service. We are extremely happy with the end result. Well done guys and thank you!”
Ray Cawston – Managing Director, Cecil & Larter