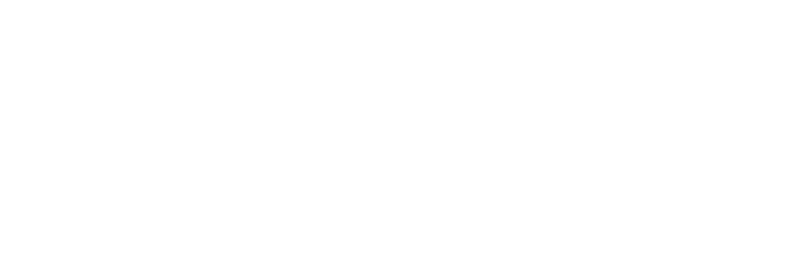
Call: 01234 765308
install and maintenance.
HOLDEN TANK FARM CASE STUDY
from Premier Garage Equipment
About our client
We were introduced to the Holden Group through our links with Volvo and had initially been asked to quote for the installation of a new VRE concept. Thanks to our reputation with Volvo and our track record of delivering liquid engineering projects, we were successful in winning this new business.
We have now worked with them for just over a year and we are excited to partner with them on their future projects.
Project brief
With three franchises on site, historically there had been three workshops, one each for Renault, Volvo and Honda. There were plans to build a showroom extension which necessitated the loss of one workshop. We were tasked with consolidating three workshops into two, combining Renault and Volvo into one. This required a rethink of oil management systems which required the correct oil grades to be routed to the correct franchise in their new locations, as well as the handling of waste oil.
Challenges we overcame
Another challenge we faced was available space onsite, which was limited. Off the shelf tanks were not suitable, so we decided to design and manufacture bespoke tanks for a perfect fit.
The project had to be completed without affecting the client’s business so we were mindful of working around technicians and structuring each stage of the project to minimise disruption. How did we do this? We designed temporary measures including waste oil points and oil supply positions and provided barrelled oil to top up reserves when necessary.
When switching to the new tank farm we timed the oil deliveries to synchronise with temporary supplies running out and arranged the changeover to suit the Holden Group’s specific needs and kept their business live throughout.
From start to finish, the project took about two weeks and was delivered on time and on budget.
The completed project
In the new tank farm, there are now four grades of oil distributed to each franchise via underground ducts, each grade in tanks with a 2,000 litre capacity. And it goes without saying that the new tank farm is fully compliant with oil storage regulations.
Measuring our success
Let’s estimate that it takes a technician a few minutes each time to collect oil from a tank or barrel that is not local to him. A workshop can see 40 services each day meaning those few minutes soon balloon to 728 hours each year. At a conservative hourly rate, this still represents many thousands of pounds potentially lost to the business. Don’t just take our word for it – large franchise dealers have long recognised this fact and commissioned studies to evidence it.
What next?
For PGE, projects like these invariably lead onto more projects with other clients, both new and existing. Thanks to our many years of experience, we have become the ‘go to’ for projects like these and we are often approached for our advice on a range of topics.
What Our Customer Had to Say
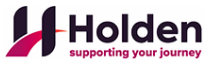
Adrian Guest - General Manager
We knew that PGE had the necessarily skills for the job but to see a potentially complicated project be delivered in just two weeks without any hiccups was impressive. There was always someone on hand to chat to and to discuss any project amendments and their ability to interpret the regulations for us and reassure us that we would be fully compliant was always appreciated. Thanks to the PGE team, the cost savings to our business are already being realised. A great supplier to partner with, we highly recommend them.”