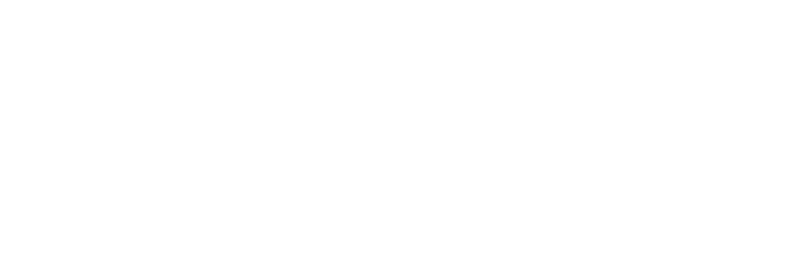
Call: 01234 765308
install and maintenance.
CITYGATE SEAT TWICKENHAM CASE STUDY
from Premier Garage Equipment
About our client
Project brief
There was a wheel alignment bay which was sorely under-utilised, but no MOT bay. Citygate asked us to create a space which combined both. They were keen to improve and increase their wheel alignment offering, so our bespoke design ensured this was addressed while incorporating a fully-specified MOT bay, both in line with current legislation.
Our top three objectives were to manage our budget, our timeline and avoid disruption to the workshop and the technicians as Citygate could not close the dealership.
Image shows old lift and wheel aligner to be replaced
Image shows groundworks taking place
Did the project present any challenges?
While the work was complex, largely thanks to the excavations left behind in the ground following the redesign, we carefully planned and co-ordinated everything, ensuring the project was delivered on time and on budget.
Working in an open, busy dealership also presents challenges; however, we have delivered countless projects in the past working in these conditions and the key to success is planning. Each day we are on site, we carefully plan which works will take place and when. We often start before the technicians arrive for the day, and we arrange deliveries either first thing in the morning or last thing in the evening to avoid disruption.
At Citygate, we had to move an existing 2-post lift which was in use; to keep it operational as long as possible, we organised our works so that it could be removed at the last minute, minimising the time it was out of action.
Every project requires collaboration with other contractors; we liaised closely with Citygate’s architects and ground workers while on site and managed their involvement in the project.
Why did Citygate choose PGE for this project?
We know that customers highly value our project management skills, the way we co-ordinate with other contractors and our ability to ensure everything runs smoothly. That’s not to say there are never issues to deal with, but those issues are ours – not the clients’ – and we rarely need to involve them in the detail.
Image shows wheel alignment bracket where cameras are mounted
How we went the extra mile
In our designs, we were keen to identify opportunities for saving Citygate money. We realised we could use their existing wheel alignment equipment rather than replace which saved thousands of pounds and designed the cabling, duct work and specs for the new lift accordingly. This never compromised the quality or compliance of the works but created a highly efficient space for the lowest budget possible.
We also oversaw the brake tester connectivity integration for DVSA, which is a regulatory requirement to stamp out fraud in the MOT industry. Brake testers must be connected to a computer and the results uploaded and sent electronically to the DVSA. While this sounds simple enough, the security processes can be complex and time consuming, and for dealers who aren’t familiar with this process, sometimes highly frustrating.
How is Citygate measuring this success?
With an in-house MOT bay, Citygate is back in control. Invariably this leads to more work from customers for servicing, maintenance and repairs.
At Citygate, the combined bay has completely solved this dilemma and productivity is increasing month on month.
Image shows new equipment being commissioned prior to use